It’s often a requirement in warehouses with busy warehousing operations to stage the goods to be loaded in an intermediate staging area and execute the loading process when a TU arrives in the warehouse.
The staging process in SAP S/4HANA EWM is usually carried out a day before the actual loading is supposed to happen, which saves loading time because any issues in the picking process can already have been handled. This reduces the unproductive process of a warehouse worker fetching the stock from a warehouse source bin for each warehouse request item separately. Instead, the warehouse worker draws the stock for multiple warehouse request items into an intermediate staging area near the loading bay or goods issue area. This is called the withdrawal step in two-step picking. In the next step, the warehouse operator creates warehouse tasks to redistribute the stock to fulfill individual warehouse requests, as shown in this figure. This step is called the allocation step in two-step picking.
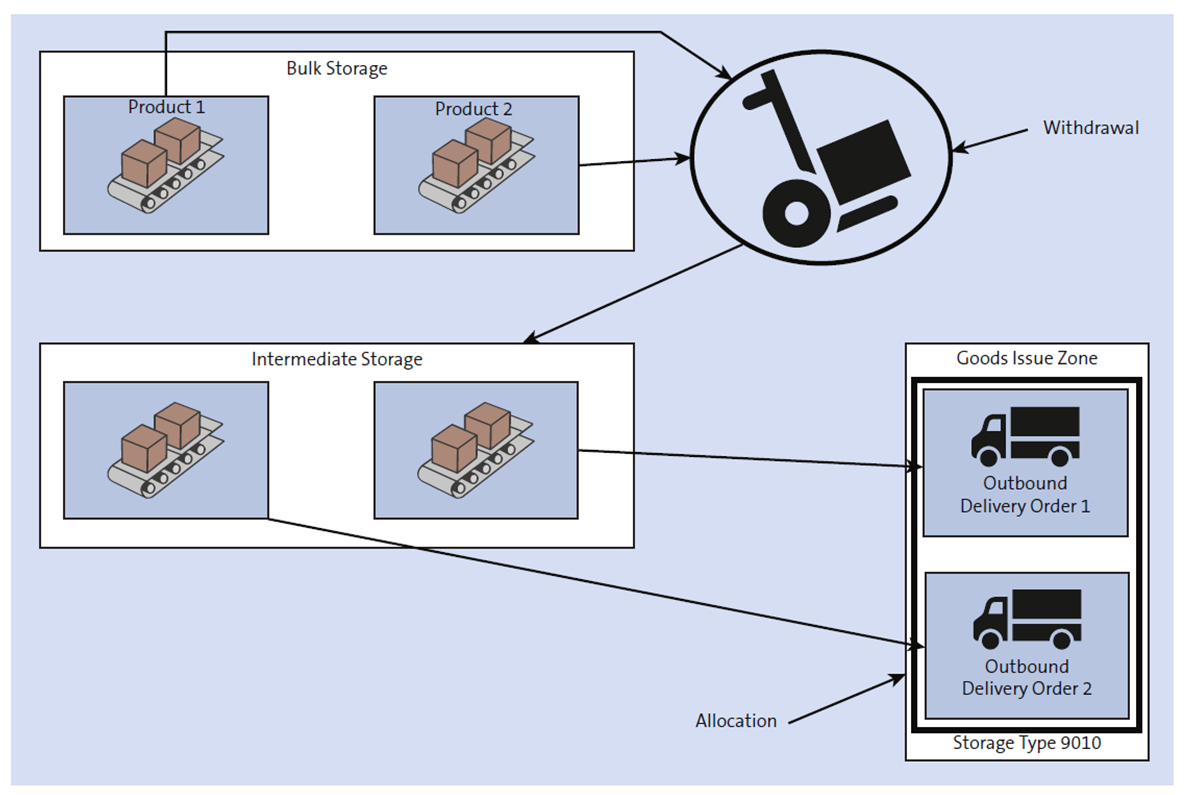
In the following sections, we’ll look at how to set up and use two-step picking.
Configuration
To activate the two-step picking process, you need to make a couple of important configuration and master data setup entries. Based on the following settings, users can set normal wave picking and wave picking configured as a two-step process in the warehouse:
- Define a warehouse process type for creating withdrawal warehouse tasks for picking. In the standard system, process type 2020 is defined for picking steps.
- Set up the relevance for two-step picking at the warehouse level. As shown in the next figure, choose Two-Step Pick from the dropdown menu for the warehouse via IMG path SCM Extended Warehouse Management > Extended Warehouse Management > Goods Issue Process > Wave Management > General Settings > Set Up Two-Step Picking. The warehouse process type used for carrying out the first step in two-step picking is specified in the Process Type In standard embedded EWM, warehouse process type 2020 is used, but you can create a different warehouse process type.

- To activate the two-step process at the product level, set the value of the control indicator for Two-Step Picking to “2” in the Whse Data tab of the product master, as shown in the next figure. This allows two-step picking to be activated only at the product level, rather than for the entire warehouse.
- The intermediate storage bin where the stock picked for outbound delivery orders is to be placed is defined in the customization settings for the warehouse process type created in step 1 by providing the destination storage type and bin in the Stor.Type and Destination Bin fields, respectively. In standard embedded EWM, storage type 2010 is used.
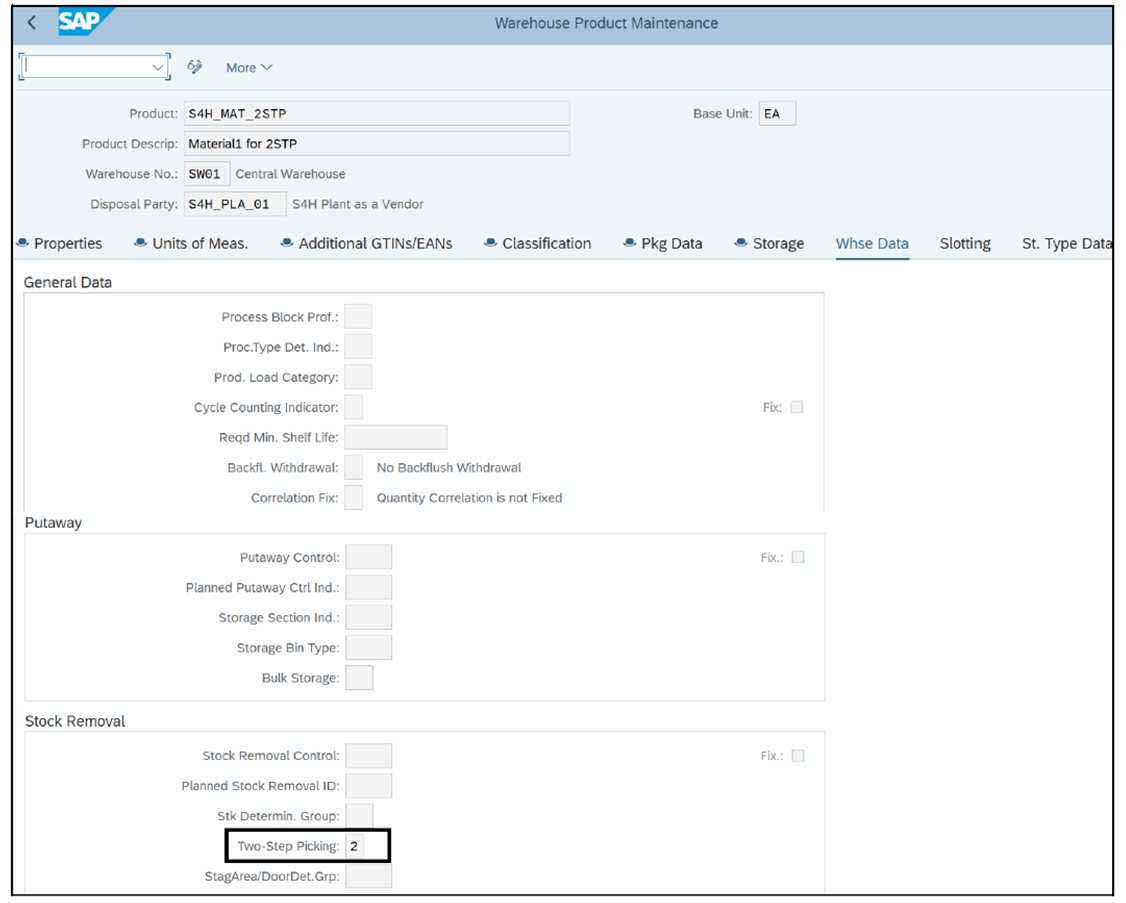
- In the optimization of the search sequence for picking, as shown below, set the indicator (checkbox under column 2) for two-step picking sequence to have the system give priority to the two-step picking process.
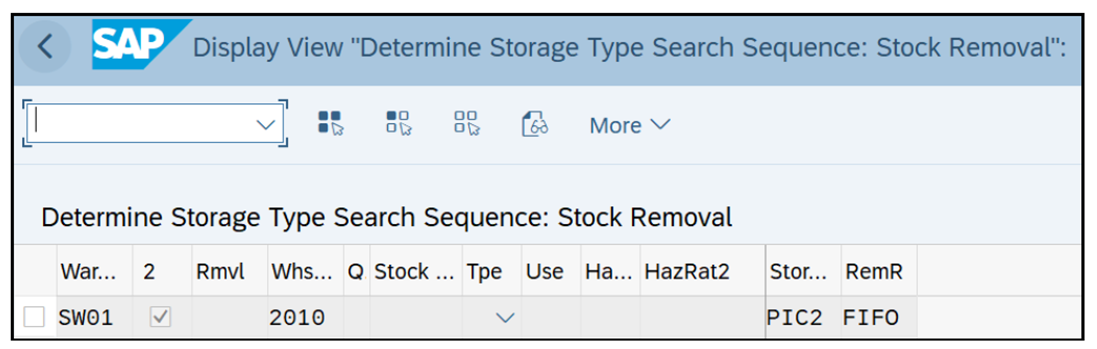
- The stock removal strategy for allocation steps must contain the interim storage type in its search sequence. To do this, specify the intermediate storage type in the storage type search sequence, which is assigned in the determination for warehouse process type 2020, and set the indicator for two-step picking.
- Ensure that all relevant storage types, sections, and bins are created for an intermediate storage type in which products will be stored after the first picking step.
Execution
In this section, we’ll discuss the two steps for carrying out two-step picking in the warehouse.
Step 1: Withdrawal
This is the step in which the stock quantity for multiple outbound delivery orders is withdrawn from the source bin in the warehouse and placed in an intermediate storage area. This step provides optimization by enabling picking for multiple outbound deliveries in one step, thus reducing the number of picking operations that need to be performed by warehouse workers. Stock picking is done from various source storage bins and placed in bins in the intermediate storage. The steps involved in the withdrawal process are as follows:
- Multiple outbound delivery items are combined into a wave.
- Embedded EWM determines the relevance of the wave for two-step picking from the configuration and master data of the product, as explained in the previous section. If required, also make a wave relevant for two-step picking by changing the value of indicator 2StP to “2” when creating a wave manually using Transaction /SCWM/WAVE.
- A withdrawal warehouse task is created for the wave using withdrawal steps by clicking on Release Withdrawal. This step can also be executed in the warehouse management monitor by selecting the required wave and choosing the Release Withdrawal option from the More Methods button, as shown in the figure below.
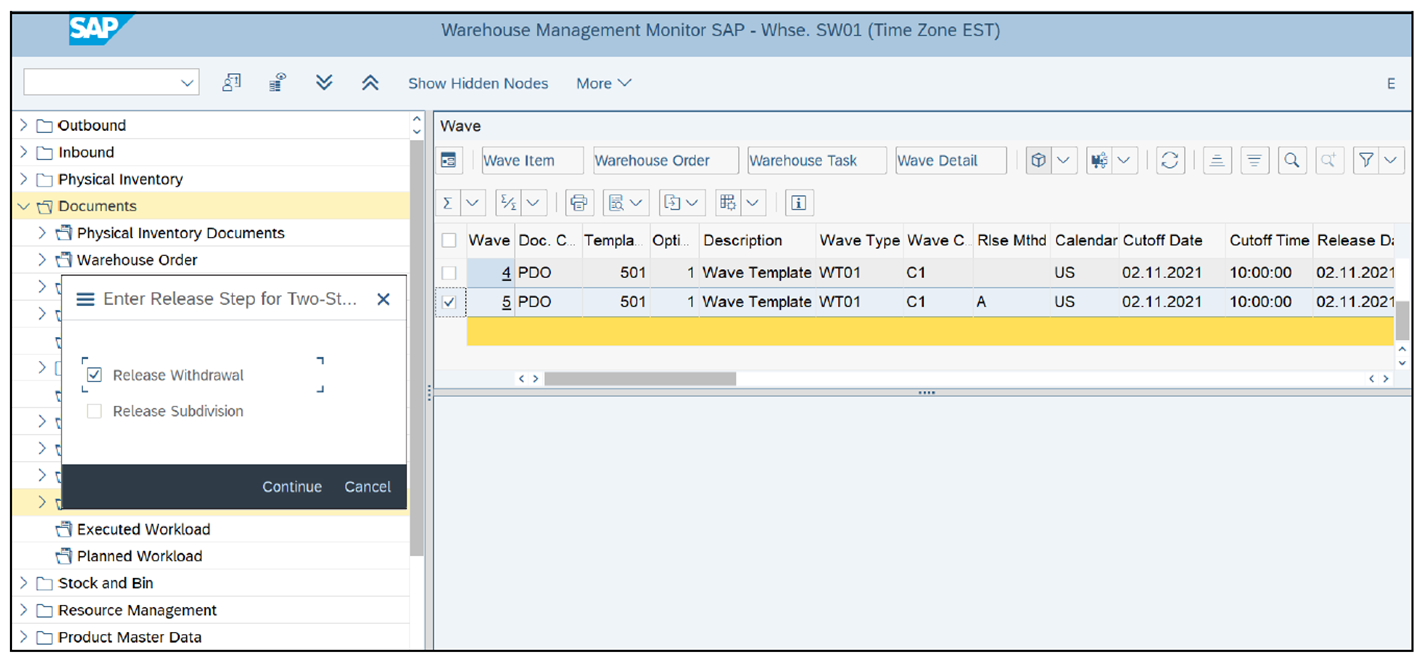
- After the warehouse task for withdrawal is created, it’s confirmed by the warehouse worker after the worker physically places the stock in the intermediate storage area.
Step 2: Allocation
In this step, stock is picked from the intermediate storage bin and distributed to individual outbound delivery orders at the time of loading. The steps involved in the allocation process are as follows:
- The next set of warehouse tasks is created from the wave maintenance screen using Transaction /SCWM/WAVE, which is then used for assigning the stock from the intermediate storage bin to individual requirement goods issue bins. The allocation warehouse task can also be created in the warehouse management monitor using Transaction /SCWM/MON. In the warehouse management monitor, the wave for the two-step process is selected, and the Release Subdivision option is selected from the More Methods button, as shown in this figure.
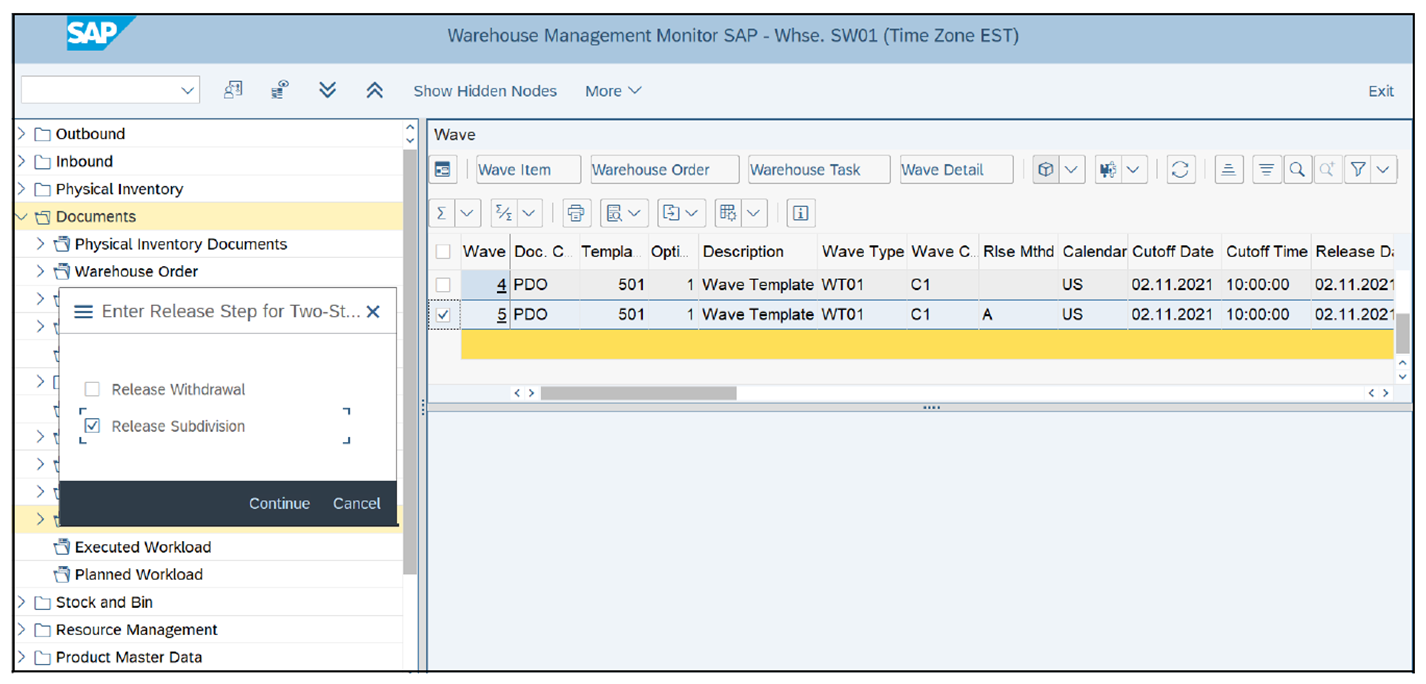
- A warehouse worker physically moves the stock from the intermediate bin to destination bins for open warehouse requests.
- After the completion of the physical movement, the warehouse worker confirms the allocation warehouse task created in step 1.
Learn SAP EWM in Our Upcoming Rheinwerk Course!
The master class on embedded EWM! Learn how SAP S/4HANA enacts key warehousing processes, from inbound and outbound to internal processing. Dig into your organizational structure, master data, and warehouse settings—and then discover how your business requirements are supported by underlying system configuration. This upcoming course in January and February is live on the web and will teach you all you need to know about these topics. Click on the banner below to learn more and order your ticket.
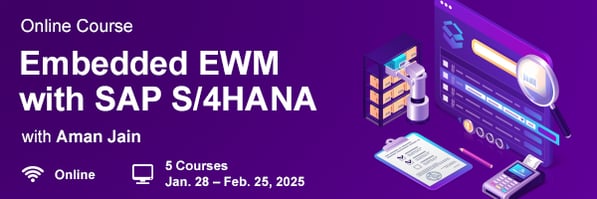
Editor’s note: This post has been adapted from a section of the book Warehouse Management with SAP S/4HANA by Namita Sachan and Aman Jain.